Control backorders with Magento
Overview
The backorder system allows you to continue to sell products on your website that are out of stock in your warehouse. Depending on the structure of your business and your supplier relationship, you may opt to display products on backorder as ‘In stock,’ or with a customized availability message such as, ‘Available in under ‘X’ days.’
With Magento and Embedded ERP efficiently facilitate backorders, handling every step of the supply chain once an out-of-stock order is placed.
We can identify two scenarios in which a backorder is necessary.
- Regular backorders : Your product is out-of-stock in your warehouse, but your supplier has it in stock. When a new order is placed for the given product, you must place a purchase order with your supplier to replenish your stock and fulfill the order.
- Consignment : Your supplier has reserved a limited quantity of products for your business and you are able to sell within this amount. Once you have sold out of your apportioned stock, you must place a purchase order to replenish it and fulfill orders.
Regular backorders
In the case of regular backorders, you may opt to display a customized availability message to inform your customer of the amount of time it will take to deliver their order, since you will have to purchase the product(s) from your supplier before they can be shipped.
In order to do this, you must first configure your Magento settings to allow your customers to purchase products that are out of stock. This preference can be made as a global setting in System> Configuration > Inventory OR Per Product.

Then, with
These configurations can be found in the Product Availability Ranges feature:


And finally, your customer is able to follow the order progress with an estimated delivery date.

Consignment
With consignment, you consider your supplier’s warehouse as your own. This means that if your product is in stock at your supplier’s warehouse, it is considered “in stock” on your website. However, once a customer order is placed, you must submit a purchase order to obtain and ship the product.
With this feature, you are able to set up two different warehouses: your own and your supplier’s. You can then import your supplier’s stock levels into the second warehouse. (This can be done automatically using the Drop Shipping extension if your supplier provides their stock levels in a csv file on an ftp server).
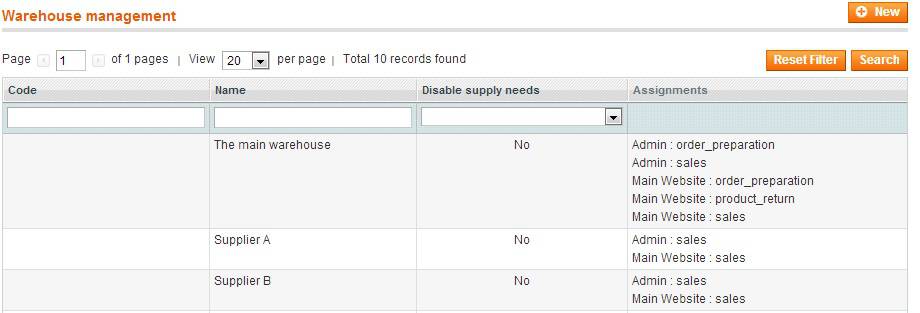
Embedded ERP uses the information from both warehouses to define product availability:
- Product in stock in your warehouse + not in stock in supplier warehouse = ‘In Stock’ on your website
- Product not in stock in your warehouse + in stock in supplier warehouse = ‘In Stock’ on your website
- Product not in stock in your warehouse + not in stock in supplier warehouse = ‘Out of Stock’ on your website
Supply Chain Control
Embedded ERP covers every step necessary to track and fulfill backorders. The workflow is as follows:
When a new order is placed, Embedded ERP scans every product ordered and reserves it in your stock. With this feature, the ERP knows which products are scheduled for shipment.
On the logistics side, orders are organized in separate tabs depending on their reservation status. If at least one product is out of stock, the order is displayed in the stockless order tab so the logistics operator knows they must wait to ship the order.
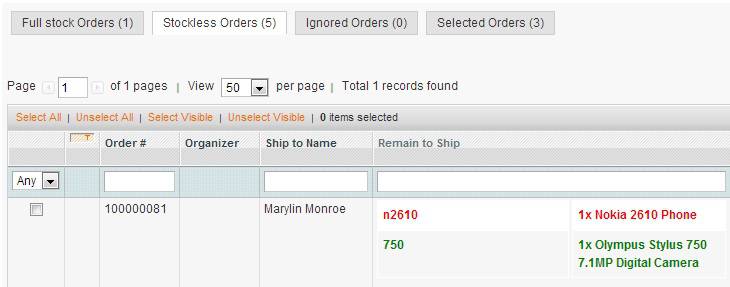
When stock levels are insufficient and Embedded ERP is unable to reserve a product, it produces a supply need indicator to inform the purchase manager that they must submit a purchase order to supply the product. The ‘Supply Needs’ page displays every product for which a purchase order is required. From this page, the purchase manager can filter the supply needs list by supplier and, with one click, create a purchase order for every product needed from the given supplier. The next step is to complete the PO (prices, additional products, etc.) and notify the supplier by email with the purchase order PDF attached.
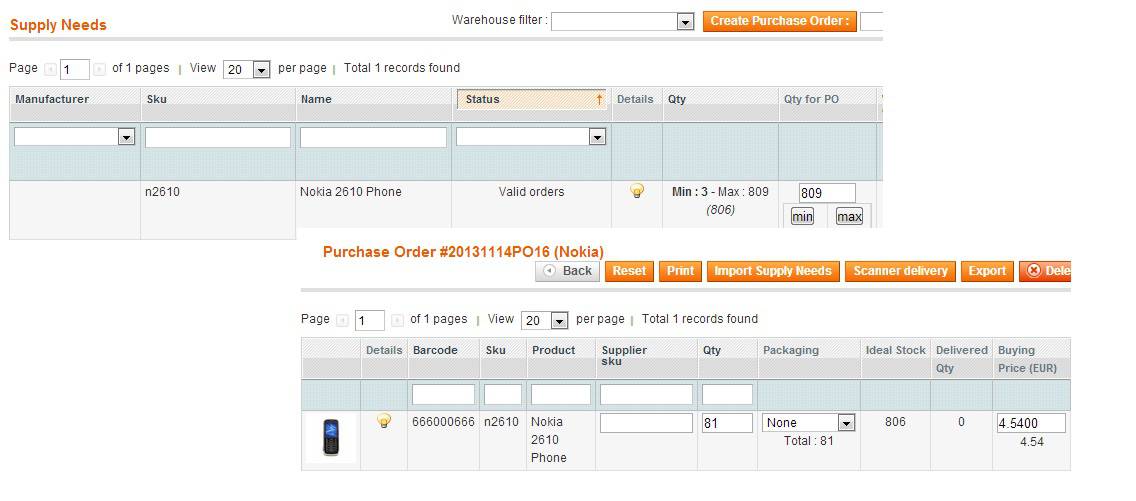
Then, once you receive the purchase order, you can confirm the delivery in Embedded ERP and automatically increase stock levels. Once this is complete, ERP verifies if there are pending orders for the products received and reserves the newly received stock to incoming orders when needed.
When product reserves are fulfilled for an order, it is then labeled ‘Shippable’ on the order preparation page and the operator can proceed in shipping the order.
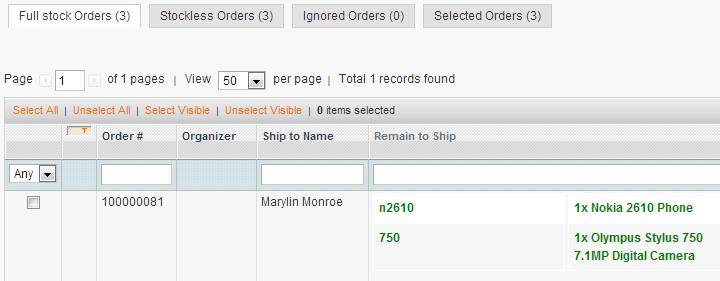
Related products
Embedded ERP M1 and Embedded ERP M2
Embedded ERP is a system of Magento extensions that manage stock, purchasing, and logistic processes from your back office.